- September 23, 2024
- Posted by: MCAM Northwest
- Category: Tech Tip
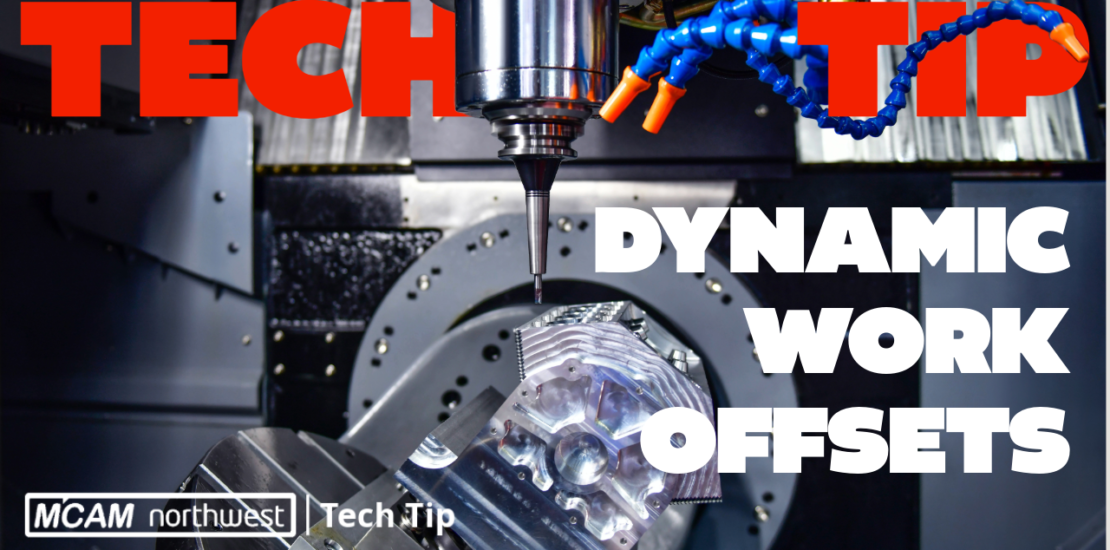
Tech Tip: Exploring Dynamic Work Offsets in CNC Machining with Mastercam
Dynamic Work Offsets (DWO), also referred to as DFO or Cycle 800, is a game-changing feature for CNC machinists using four or five-axis machines. But what exactly does it do, and how can it simplify your machining processes? In this Mastercam Tech Tip, we’ll break down what DWO is, why it’s important, and how you can take advantage of it in Mastercam.
How do Dynamic Work Offsets (DWOs) improve efficiency in Mastercam?
Using DWO in Mastercam enhances efficiency, reduces programming complexity, and minimizes errors, leading to faster production turnaround times. Embracing DWO can significantly improve your machining operations.
What is a Dynamic Work Offset and Why Should You Use It?
Dynamic Work Offsets (DWO) allow you to set your zero point (the machine’s reference point for cutting) in a location that isn’t the machine’s rotary center. This is essential when working on parts where aligning the center of rotation isn’t practical, such as setting the zero on a part’s corner or another easily accessible feature.
For machinists who need to rotate parts to multiple rotary positions, DWO ensures that the machine can accurately track the part’s position across all axes, making setup and programming far simpler. This feature significantly reduces the workload for both programmers and operators by streamlining the alignment process.
DWO is especially useful when:
- You can’t center your part on the table.
- You prefer to set the zero on a corner or other feature for easier probing.
- You need to rotate the part to multiple positions while keeping the machine aligned with minimal effort.
How Does DWO Simplify Machining?
Let’s walk through an example: (make sure to watch the full Tech Tip video above!)
Without DWO:
When you program without DWO, you’ll need to align all toolpaths with the machine’s center of rotation. For instance, in your posted code, you might see your X and Z values remain unchanged across rotary positions. Everything stays aligned with the machine’s fixed rotary center.
With DWO Enabled:
The beauty of DWO is in its simplicity. After enabling it, you can program your part much like you would for basic three-axis work. You simply set your zero at a convenient point on the part, and DWO handles the rest—adjusting for rotation and keeping everything aligned.
For positional work, DWO allows you to return to the mindset of programming without worrying about rotary axes. This not only makes programming easier but also reduces the potential for errors during setup and machining.
Getting Started with DWO in Mastercam
To start using DWO, follow these steps:
1. Purchase and Enable DWO on Your Machine
DWO is usually an optional feature that needs to be enabled on your machine. If your machine doesn’t support it, contact your machine reseller to get it installed.
2. Check Your Post
DWO needs to be supported by your post-processor. This step ensures that your Mastercam software will communicate with the machine properly to use DWO.
In Mastercam, search for DWO in your post. For example, you can use the “CTRL+F” function in Code Expert to find it. If you find a line indicating “Control supports DWO,” but it’s set to “No,” you’ll need to change it to “Yes” to enable the feature. (Note, this can change quite a bit depending on who made your post. Reach out to MCAM Northwest if you have any questions about your particular post.)
3. Programming with DWO
Once DWO is enabled, you’ll have more flexibility. You can now set your zero point anywhere on the part, such as on the part’s corner, which might be a more convenient place to probe during setup. This is especially useful when dealing with irregular or large parts where centering isn’t feasible.
Dynamic Work Offsets offer a powerful way to simplify your CNC programming and setup. By allowing you to set your zero in more convenient locations and automatically compensating for rotations, DWO reduces the complexity of multi-axis machining. If your machine supports it, enabling DWO can save you time and improve the accuracy of your setups.
Another note to make here is that we’ve been using DWO as a proxy for a larger group of cycle options in this article. Other manufacturers call this Tilted Work Planes, Cycle 800, or simply G68.2. These options may be slightly different from each other, and some have advantages over others. This all comes down to the machine and controller manufacturers. It’s always a great idea to speak with your machine sales rep to find out what options are available to you and what options might make you more efficient in the shop.
Need help setting up DWO or modifying your post to support it? Contact MCAM Northwest at 503-653-5332, or email us at sales@mcamnw.com and we’ll be happy to assist you!
Follow our Tech Tip series for more Mastercam tips and tricks.
Key Takeaways (TL;DR)
- Simplified Setup: Dynamic Work Offsets (DWO) allow machinists to set zero points at convenient locations on parts, reducing the complexity of alignment and setup.
- Improved Efficiency: By enabling accurate tracking of part positions during rotation, DWO minimizes programming time and enhances overall machining productivity.
- Enhanced Accuracy: DWO ensures that all toolpaths are aligned correctly, maintaining precision even when parts are positioned away from the machine’s center of rotation.
- Easy Integration with Mastercam: Implementing DWO in Mastercam is straightforward. Contact MCAM Northwest with any questions!
Follow MCAM Northwest!
LinkedIn: mcam-northwest
YouTube: The MCAM Northwest
Facebook: @MCAMNorthwest
Instagram: @mcamnorthwest
X (formerly Twitter): @MCAM_NW
Come see us in person! Visit our Events page to see where we are headed next.