- June 24, 2024
- Posted by: MCAM Northwest
- Categories: Mastercam, Product Spotlight
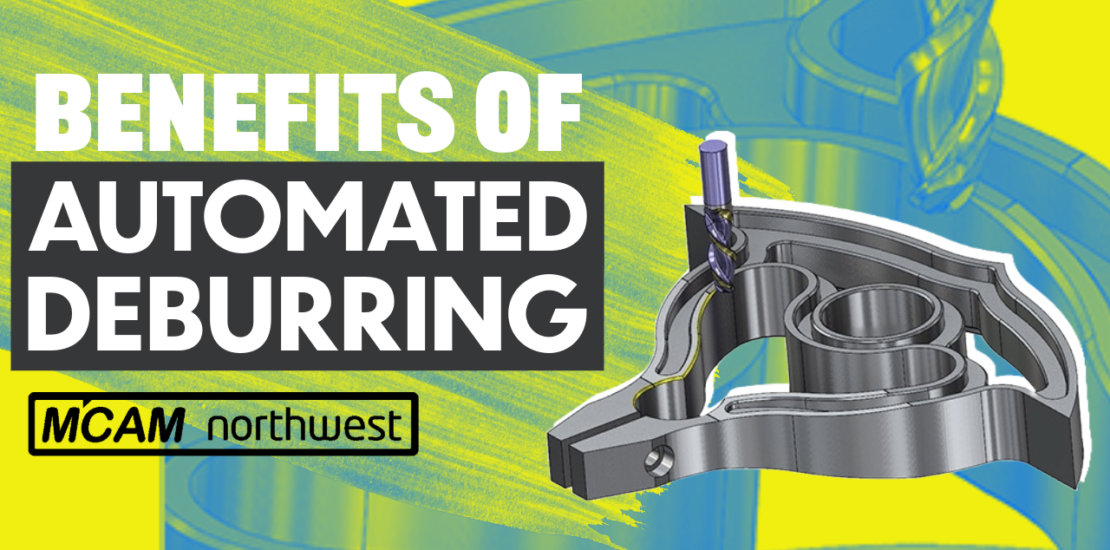
The Advantages of Automated Deburring in CNC Machining
Imagine if you could significantly reduce post processing time, ensure perfect consistency, and enhance the safety and appearance of your parts—all without lifting a finger. Welcome to the future of manufacturing with automated deburring. In this blog, we’ll explore how automated deburring offers unparalleled advantages over traditional manual methods, setting new standards for quality and efficiency.
What are the benefits of automated deburring in CNC machining?
Key advantages of automated deburring in CNC machining include time savings, consistent improvements, reduced scrap rates, reduced chances for injuries, and more professional-looking results.
6 Benefits of Automated Deburring
A critical finishing step in CNC machining, deburring was traditionally performed manually, but with advancements in technology, automated deburring has become increasingly popular. Some of the benefits that automated deburring offers include:
#1 Time Savings
One of the most significant advantages of automated deburring is the substantial time savings it offers. Manual deburring is a labor-intensive process that can be slow and tedious, especially for complex parts with intricate geometries. Automated deburring, on the other hand, can process parts much faster and with greater efficiency. CNC machines are designed to handle high volumes and can work continuously without breaks, significantly reducing the overall production time. This increase in productivity allows manufacturers to meet tight deadlines and increase throughput without compromising quality.
#2 Consistent Improvements
Consistency is crucial in manufacturing, and automated deburring delivers in spades. Human workers, no matter how skilled, can introduce variability into the process due to fatigue, concentration lapses, or varying levels of expertise. Automated systems, however, provide uniform results every time. They are programmed to follow precise instructions and can repeat the same operation with high accuracy. This consistency ensures that every part meets the exact specifications and quality standards required, reducing the need for rework and enhancing overall product reliability.
#3 Reduced Scrap Rates
Scrap rates can be a significant drain on resources and profitability in CNC machining. Manual deburring, with its inherent variability, can lead to inconsistencies that result in parts being rejected. Automated deburring minimizes these risks by providing a more reliable and predictable process. The precision and repeatability of automated systems mean that parts are less likely to be damaged during the deburring process, thus reducing the amount of scrap generated. Lower scrap rates translate into cost savings and more efficient use of materials.
#4 Reduced Chances for Injuries
Safety is a paramount concern in any manufacturing environment. Manual deburring involves the use of handheld tools, which can be hazardous and lead to injuries such as cuts, repetitive strain injuries, and other musculoskeletal disorders. Automated deburring significantly reduces these risks by eliminating the need for human operators to perform dangerous tasks. Machines can handle the sharp edges and repetitive motions that pose risks to workers, creating a safer workplace and reducing the likelihood of injury-related downtime and compensation claims.
#5 More Professional Looking Results
The final appearance of machined parts is crucial, especially for industries where aesthetics and precision are critical. Automated deburring systems provide a superior finish compared to manual methods. They can achieve smoother edges and surfaces, ensuring that the parts look professional and meet stringent quality standards. When you need to compete with other shops putting out accurate parts, having a leg up on aesthetics and smooth edges can win the account.
#6 In Process Deburring
Deburring automation allows programmers to deburr a part’s edges that must be clean and burr free for subsequent fixturing or work holding, say in the case of a part flip from Op1 to Op2. This is necessary for auto attended (Robotic) part handling and placement where a previously cut edge with a burr might interfere with the work holding.
Different Types of Deburring Tools
Automated deburring in CNC machining centers can be performed using a variety of tools, each suited to different applications and part geometries. Here are some common deburring tools used in CNC machining:
Ball Endmills: These tools are excellent starter tools for deburring as they are typically already found in many machines for other operations. They can be used to access sharp edges in 3-axis mills from the topside.
Lollipop Tools: Named for their shape, lollipop tools are useful for reaching into hard-to-access areas and internal features of parts. They can efficiently deburr undercuts and tight spaces that other tools might miss. Lollipop tools are an excellent all-round deburring tool.
Chamfer Mills: Chamfer mills are designed to create bevels or chamfers on edges. They are perfect for deburring straight edges and creating uniform beveled edges that enhance the appearance and functionality of the part. In a multiaxis machine, these tools can be used on almost all sharp edges with proper access.
Dovetail Cutters: These cutters are used for deburring dovetail slots and other angled features. They provide precision and control, ensuring clean and accurate finishes on these specific geometries. Dovetail cutters excel at reaching the underside of thru features.
Ceramic Fiber Tools: Known for their durability and ability to handle high temperatures, ceramic fiber tools are excellent for deburring all sorts of materials. These tools can deburr quickly and efficiently, often faster than traditional carbide tools, and can tend to leave a cleaner, sharper corner than other tools while still removing the burr itself.
Standard Endmills with Mastercam’s Deburr Toolpath: Standard endmills can also be utilized for deburring in multiaxis machines with the use of Mastercam’s Deburr toolpath. This toolpath allows for precise control over the deburring process, enabling standard endmills to perform complex deburring tasks with ease. The Deburr toolpath is capable of using all of the tools above in addition to flat endmills, chamfered endmills, bull nosed endmills, and tapered endmills.
4 Ways to Start Deburring with Mastercam
1 – Model Chamfer Toolpath: The Model Chamfer toolpath is excellent for removing burrs on top side edges in 3 axis environments.
2 – Contour: Contour has a chamfer option which can be used to deburr parts in 2D and 3D. Contour also has a corner break option to help deburr exterior corners.
3 – Deburr 3-Axis: The new Deburr 3D add on for Mastercam 2025 allows for 3D only access to the famous Deburr toolpath from Multiaixs. This new add-on is a low cost entry into deburring that is more intelligent than the options above. (Watch our Tech Tip to learn more!)
4 – Multiaixs Deburr Toolpath: The Multiaixs Deburr toolpath takes advantage of a wide variety of tools to deburr nearly any sharp edge with a high degree of control. This is the most flexible option that can work in 3, 4, or 5 axis scenarios as well as Mill-turn applications.
From time savings and consistent improvements to reduced scrap rates and enhanced safety, the benefits of automated deburring are clear. By embracing automated deburring and utilizing the right tools, companies can streamline their operations, protect their workforce, and deliver high-quality products that meet the demands of modern industry. Are you ready to try automated deburring? Reach out to our Sales Team!
Key takeaways (TL;DR)
- Substantial Time Savings: Automated deburring significantly enhances overall efficiency and productivity, without compromising quality.
- Consistency in Quality: This precision and repeatability lead to parts that consistently meet exact specifications and quality standards.
- Lower Scrap Rates: Minimize the risk of damaging parts, reducing scrap rates and resulting in cost savings and more efficient use of materials.
- Enhanced Safety: By eliminating the need for manual handling of sharp edges and repetitive motions, automated deburring reduces the risk of injuries, creating a safer workplace and lowering the likelihood of injury-related downtime.
- Professional Finish: Automated deburring systems deliver superior finishes, achieving smoother edges and surfaces compared to manual methods.
Follow MCAM Northwest!
Facebook: @MCAMNorthwest
LinkedIn: mcam-northwest
X (formerly Twitter): @MCAM_NW
YouTube: The MCAM Northwest