- September 24, 2024
- Posted by: MCAM Northwest
- Category: Mastercam
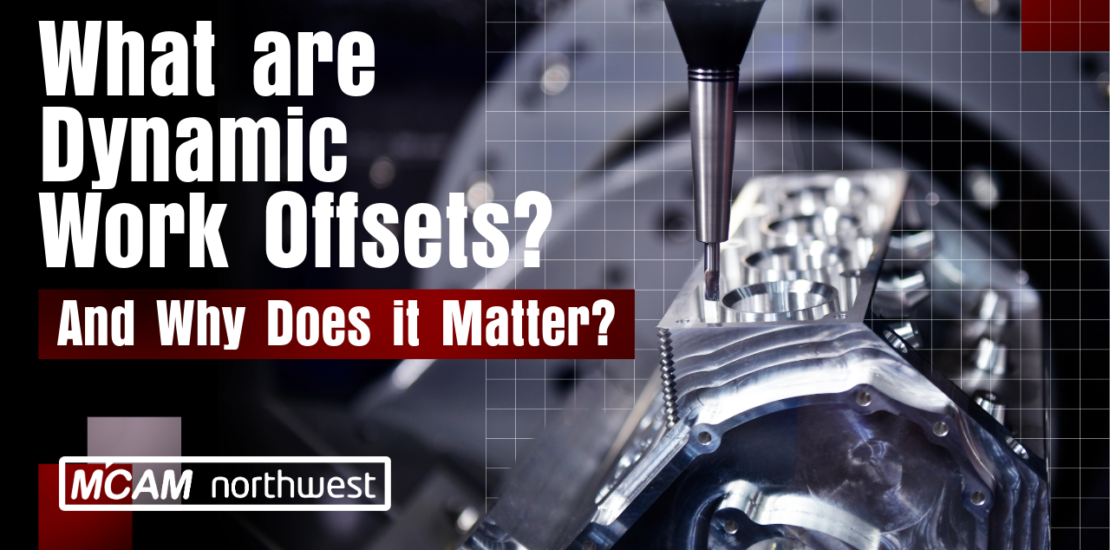
What are Dynamic Work Offsets, and Why Does it Matter?
Dynamic Work Offsets (DWO), also called DFO or Cycle 800, is a feature for 4-axis and 5-axis CNC machines that simplifies setups by allowing the work offset zero to be placed anywhere, not just at the center of rotation.
This technology tracks the zero point as the rotary axis moves, making machining more flexible and efficient. For manufacturers, DWO is a valuable option that saves time and improves precision.
Unlock the full potential of your 4-axis and 5-axis machines with Dynamic Work Offsets—streamline setups, boost precision, and take your productivity to new heights!
What are Dynamic Work Offsets (DWO) in CNC machining, and why are they important?
Dynamic Work Offsets (DWO) let 4-axis and 5-axis CNC machines set the zero point away from the center of rotation. It tracks the zero as the rotary axis moves, ensuring precision and flexibility, reducing setup time, and boosting productivity—essential for modern manufacturing.
What Are Dynamic Work Offsets?
Dynamic Work Offset, or DWO, is a software feature in your control that makes setting up 4 and 5-axis jobs easier. In traditional 3-axis machining, setting a work offset involves defining a zero point along the X, Y, and Z axes, from which the machine references its cutting movements. Dynamic Work Offsets take this concept a step further by accounting for the additional complexity of rotary axes in 4-axis and 5-axis machines.
Benefits of Dynamic Work Offsets
Dynamic Work Offsets (DWO), allow operators to place parts and fixtures anywhere on the machine’s table or platter. This makes DWO very useful for situations where the part cannot be placed centered on the center of rotation, or there is no good way to indicate the part into place.
DWO proves particularly useful when combined with probing systems, as they can automate much of the setup process. By leveling the part and setting the zero point with a probe, the operator can quickly proceed with machining. DWO removes the need for time-consuming adjustments and ensures accurate results even when the workpiece is offset.
By allowing flexibility in where the work offset is defined and maintaining accuracy as the rotary axis moves, DWO enhances productivity, reduces errors, and cuts down on machine setup time.
How Mastercam Handles Dynamic Work Offsets
In Mastercam, using Dynamic Work Offsets is fairly straightforward. First, ensure your post processor supports DWO, which can be added to existing posts for a reasonable fee by your post developer. All new posts that we provide for 4 or 5 axis include this feature.
Next, set your Work Coordinate System (WCS) and Tool Plane origin(s) wherever it makes sense. You’re not limited to placing the part at the center of rotation; instead, pick the spot that’s most practical for your specific component. The system will generate the required DWO codes, enabling the machine to adapt to your designated zero point, resulting in a smooth and hassle-free process.
Dynamic Work Offsets offer a seemingly straightforward yet remarkably efficient approach to simplify setups in 4-axis and 5-axis machining. Regardless of whether you’re acquiring new equipment or upgrading existing systems, integrating DWO is a wise choice for manufacturers seeking to refine their CNC operations.
Want to learn more about Dynamic Work Offsets? Reach out to our Sales Team!
Key takeaways (TL;DR)
- Dynamic Work Offsets (DWO) allow flexible placement of the work offset zero, not limited to the center of rotation, making setups easier.
- DWO automatically tracks the zero point as the rotary axis moves, ensuring precision in complex 4-axis and 5-axis machining.
- Reduced setup time and increased efficiency make DWO an essential feature for maximizing CNC machine productivity.
- DWO integrates seamlessly with probing systems and Mastercam, offering streamlined, error-free workflows.
Follow MCAM Northwest!
LinkedIn: mcam-northwest
YouTube: The MCAM Northwest
Facebook: @MCAMNorthwest
X (formerly Twitter): @MCAM_NW