- May 23, 2024
- Posted by: MCAM Northwest
- Category: Mastercam
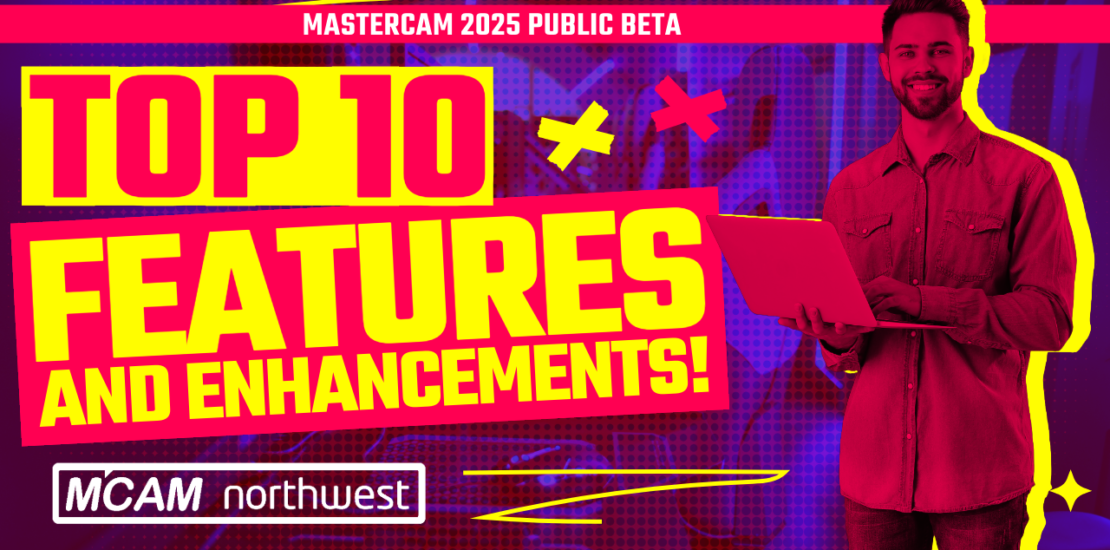
Mastercam 2025 Public Beta: 10 Features to Explore
From Y-Axis turning to the new Deburr 3-Axis Toolpath Add-on, Mastercam 2025 is packed with innovative tools and functionalities designed to empower you and your business. Join us as we delve into these exciting features and explore how they can transform your machining workflow and elevate productivity.
What are the key highlights showcased in the Mastercam 2025 Public Beta?
A few of the top 10 highlights from Mastercam 2025 Public Beta include visual linking for 2D and 3D toolpaths, finish passes for dynamic mill, y-axis turning, deviation analysis, deburr 3-axis toolpath add-on, and swarf milling with the tip of the tool.
1. Visual Linking for 2D and 3D Toolpaths
By providing a clear, intuitive representation of linking parameters directly on-screen, these markers offer a comprehensive overview of tool paths. Advancements in 2025 further enhance the experience, such as with the OptiRough tool path. By displaying minimum and maximum depth markers for steep and shallow features, users gain precise understanding and control over their machining processes.
2. Finish Passes for Dynamic Mill
The capability to include finish passes within 2D Dynamic Mill and Area Mill toolpaths enables users to add Contour style finishing passes along designated boundaries of the toolpath, significantly enhancing precision and surface quality. Programmers can fine-tune parameters such as feed rate and spindle speed overrides to optimize the finishing process. Additionally, the Lead In/Out page offers tailored lead-in and lead-out options exclusively for finish passes.
3. Y-Axis Turning
Expanding the range of machining possibilities for turning operations, Y-Axis turning allows users to utilize tools with a unique orientation, directing cutting forces more effectively into the spindle for enhanced stability and productivity. By redistributing the cutting motion, Y-axis turning optimizes the rigidity of the entire setup, allowing users to access previously difficult-to-machine areas
4. Deviation Analysis
This feature streamlines the process of surface alignment and verification, offering invaluable assistance in comparing surfaces for machining operations. By selecting reference and target surfaces, users can effectively analyze deviations between them, ensuring precision and accuracy in machining processes. By scrutinizing the deviation analysis results, displayed visually with color-coded points, users can confidently assess the compatibility of their created surfaces with the original model.
5. Saving the Machine Configurations for Mill-Turn
This new functionality streamlines the setup process by allowing users to save a variety of setups, such as tool configurations, chuck information, jaw setups, and tooling blocks, into a single file for future use. Once a user has established their preferred setup, they can save it for easy retrieval in subsequent projects. This capability offers a more efficient and standardized approach to machine setup, ultimately saving valuable time and effort. Multiple configurations can also be saved for machines that have more than one standard setup.
6. Mastercam Deburr
This innovative tool path add-on enables users to efficiently remove burrs from their parts without the need for a Multiaxis license. With intuitive controls and automatic edge detection, users can easily define the geometry to be deburred. The toolpath is compatible with ball end mills and lollipop tools, offering versatility in tool selection. By automating the deburring process, this add-on significantly reduces programming time and simplifies the creation of clean, deburred edges on parts for users without a Multiaxis add-on package.
7. Improved Associativity For Toolpaths Against Mesh Models
Previously, modifying a mesh model often resulted in the loss of associativity with toolpaths, requiring tedious reconfiguration. However, with the new improvements, toolpaths now maintain their associativity even when the mesh model is modified. This means that any changes made to the mesh, such as refining its surface, automatically update the associated toolpaths accordingly. This enhanced associativity streamlines the programming process and ensures that toolpaths accurately reflect any modifications made to the mesh model, providing greater efficiency and precision.
8. Swarf Milling With the Tip of the Tool
Mastercam 2025 introduces a groundbreaking feature for swarf milling: the ability to cut with the tip of the tool, expanding the versatility of this machining strategy. Utilizing the tip of the tool for swarf milling offers unique advantages, particularly in complex geometries. Whether it’s creating multi-axis chamfers or intricate chamfered features, the ability to utilize the tip of the tool enhances flexibility and opens up new possibilities for applying swarf milling strategies.
9. Workholding Updates
Mastercam 2025 introduces significant updates to workholding for Mill and Router groups, enhancing both machine group setup and toolpath management. Now, within the machine group setup, the workholding page allows users to manage fixtures with checkboxes to turn them on or off and the ability to group them for better organization. Additionally, the new workholding geometry group in the model geometry page simplifies the process of avoiding fixtures during toolpath creation, ensuring more efficient and accurate machining. These enhancements streamline the workflow, making it easier to manage complex machining setups and improve overall productivity.
10. A-axis Turning
The new A-axis Contour toolpath marks a significant enhancement for turning operations on B-axis style mill-turn machines with milling spindles that can index to specific angles. This dynamic rotation capability allows for deeper and more precise cuts, making it easier to reach intricate areas. The A-axis Contour toolpath opens up new possibilities for machining operations.
BONUS
11. Updates to Solid Hole Selection
In Mastercam 2025, significant updates have been made to the way solid holes are selected and used. This new feature allows users to select a hole and instantly access its entire geometry and history, simplifying programming. This enhanced selection process is not only more intuitive but also allows for condensing multiple drilling toolpaths into one, based on the varied hole geometries. The interface has been improved to manage these selections more effectively, including a dropdown for managing different types of holes within the same toolpath.
12. Safety Zone enhancements
Safety zones are now calculated as meshes in the background, whether using rectangular, cylindrical, or spherical shapes. Users can now leverage additional fields, such as linear tolerance, which allows for fewer breaks and more efficient toolpaths, and blwnding and smoothing tolerances which help to distribute and control vector changes. Safety Zone can now also read the reading maximum feed rates directly from the machine definition for the feed rate field, which ensures compliance with machine capabilities. The enhancements to the Safety Zone feature significantly improve multiaxis holemaking operations by providing smoother and more controlled tool movements.
While we’ve covered some exciting updates, there’s much more to discover! Make sure to subscribe to our YouTube channel for our webinar series where we will further demonstrate how these features work and how to apply them in your own shops. If you want to learn more about Mastercam 2025, feel free to contact us at 503-653-5332 or email us at sales@mcamnw.com.
Key takeaways (TL;DR)
- Mastercam 2025 introduces significant updates to workholding for Mill and Router groups, allowing better organization and management of fixtures.
- Mastercam 2025 enhances the visualization of 2D and 3D toolpaths by providing intuitive, on-screen representations of linking parameters.
- The new deburr 3-axis toolpath add-on allows users to remove burrs from parts efficiently without needing a Multiaxis license.
- The introduction of A/Y-axis turning expands the range of machining possibilities. This feature allows tools to operate with a unique orientation, optimizing stability and productivity by effectively directing cutting forces into the spindle, thereby accessing previously difficult-to-machine areas.
Follow MCAM Northwest!
Facebook: @MCAMNorthwest
LinkedIn: mcam-northwest
Twitter: @MCAM_NW
YouTube: The MCAM Northwest
Come see us in person! Visit our Events page to see where we are headed next.