- February 11, 2020
- Posted by: MCAM Northwest
- Categories: Insights, Mastercam
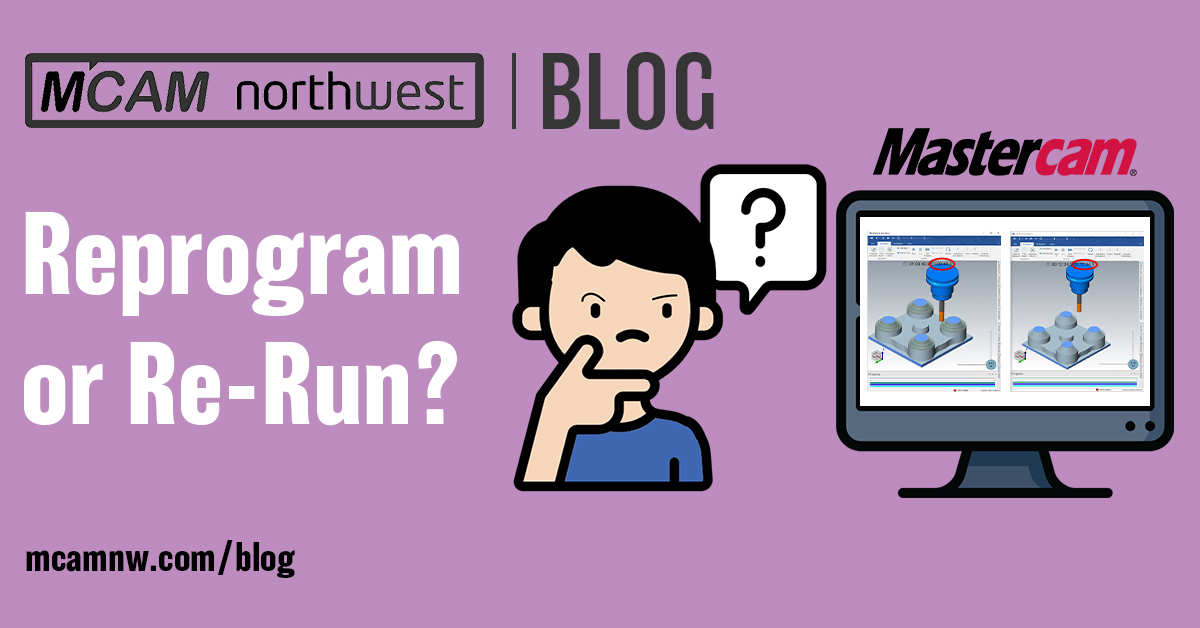
“We have been doing it this way for 30 years, why would I change it?” In the latest MCAM Northwest blog, we explore the importance of auditing your part programs and knowing when it’s time to change them.
February 11, 2020
By John Stauffer
I remember when I was working in a shop, and I noticed some programs were not running as well as I thought they could. I saw shallow step downs and full radial engagement with endmills, high speed steel drills, and inserts that would burn up after just a few parts. I had mentioned to the programmer at the time that it might be a good idea to take a look at some of these programs that had been around a long time. He responded to me,
“We have been doing it this way for 30 years, why would I change it?”
At the time, I suppose I didn’t want to challenge him because he was my senior by quite a bit, so I didn’t push the issue. I watched as that shop burned through time and money running the same programs over and over again.
I wanted to make things better, I wanted to see our shop do well. I spent some time learning Mastercam and researching tooling. I found out about the big changes that have happened in programming, and how carbide technology looks nothing like it did even 10 years ago. When we got a new programmer in the office, I convinced him to try to change up a few things and see what we could do.
After implementing modern toolpaths and trying out some new tools, we saw cycle times plummet and our lead time cut in half. Operators could barely keep up with the new programs, and we had to start thinking about how to keep the machines moving. We had to hire people because our crew couldn’t keep up with production. Our Christmas bonuses were massive compared to previous years. I kept asking myself,
“Why didn’t we do this sooner?”
When a shop has been doing something a certain way for a long time, it can be difficult to start this process. There might be hundreds of programs that would need reprogramming if things changed, so it is often thought that it would be better to keep things going as they were. With the reluctance to learn new things and test out new products, stagnation creeps in and digs into profits in this competitive market.
Let’s take a minute to look at this example. We have a legacy program with shallow stepdowns and heavy radial engagement. This was considered a good program back in the day. There are two toolpaths used to rough out this material using the same tool. There are points where the tool cuts at full radial engagement, wearing out the tool quickly. After producing a couple of these parts, the endmill tip wears out, and much of the flute length is untouched. The cycle time is just over an hour for one of these parts.
Now, look at a modern toolpath using quality carbide endmills. The depth of cut is the full length of the flute with small radial engagement. By implementing radial chip thinning and the speeds and feeds that are meant for this type of cutting, we increased our feed rate three-fold. By stepping up to mill the geometry, we extend the tool life drastically as well. Our cycle time is down to about 13 minutes. Over the course of a 25-piece job, that saves 19.5 hours of machine time!
I do want to mention that this is not always the case. There have been times where reprogramming has led to only minor cycle time decreases, and when only a few of those parts get run per year, it didn’t justify the time it took to reprogram it. There are a lot of factors to consider when thinking about reprogramming, and they shouldn’t be taken lightly. This is a competitive industry, and spending hours reprogramming a part that will only save a little time or money is not cost effective. With that in mind, we want to offer you some insight in making this decision.
We will be hosting a live webinar Reprogram or Re-Run? that will premiere this Thursday (February 13th) at 10:00 AM to walk you through the key factors to consider when debating whether or not to reprogram a part. You can sign up for the webinar here. During the webinar, will also be providing a download link to a spreadsheet where you can estimate reprogramming time, and use your real shop rates to help determine the cost of your jobs. It will show you the difference that you can make on your real cost, based on how many parts you will run, and the cost of reprogramming them.
Follow MCAM Northwest!
Facebook: @MCAMNorthwest
LinkedIn: mcam-northwest
Twitter: @MCAM_NW
YouTube: The MCAM Northwest
To view and register for upcoming MCAM Northwest webinars, visit our Events page!