- June 29, 2023
- Posted by: MCAM Northwest
- Category: Insights
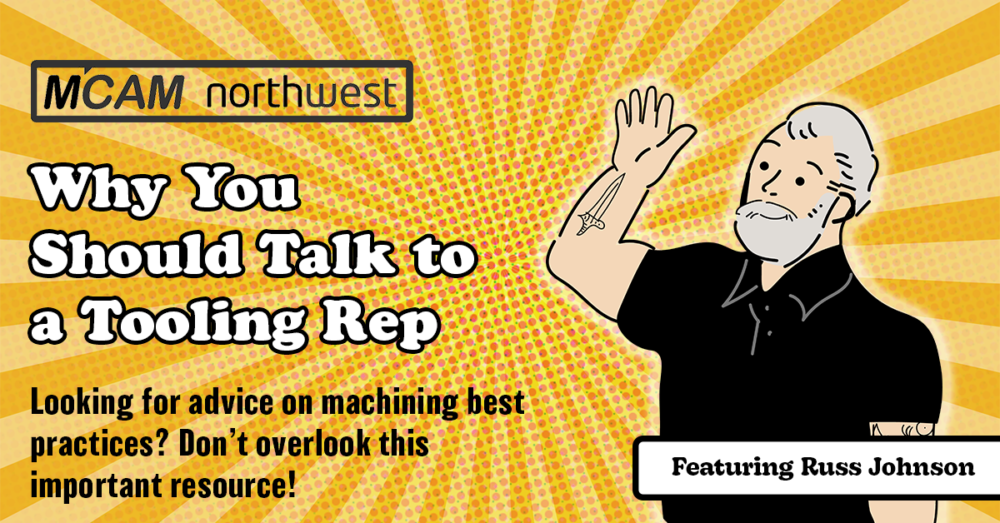
Looking for ways to machine better? Talk to your Tooling Representative!
By Callie Morgan
Thursday, June 29th, 2023, 1:45 PM PDT
Russ Johnson has been a tooling representative at Western Tool & Supply Company for over 10 years. Tooling Sales Representatives’ primary job is to promote and sell tooling products for CNC machines. However, Russ’ role does not involve crunching together price quotes and crafting sales pitches. He helps manufacturers save money, maintain and earn new jobs with the machining advice he provides.
Russ leverages his over 30 years of machining and Mastercam CAD/CAM experience to help manufacturers across Oregon and Washington fine tune their process to maintain job contracts and win new ones.
Russ shared with us the kinds of machining problems he helps solve on a daily basis and the importance of reaching out to your tooling representative as a resource.
“Why wouldn’t you want a journeyman with a lot of experience to help you?” said Russ. “You need a tool rep because you want to be more productive, you want to know how to use the tool you are buying, and buy quality tools.”
The Machining Sandwich Checklist
Russ’ primary job is to drive out to customers and help them resolve tooling issues. To troubleshoot, Russ uses a checklist he calls the Machining Sandwich. The sandwich is a way to visualize the components of a CNC machine stacked in a hierarchy of importance.
“The tool is hardly ever the problem,” said Russ. “The other things in the sandwich are the problem.”
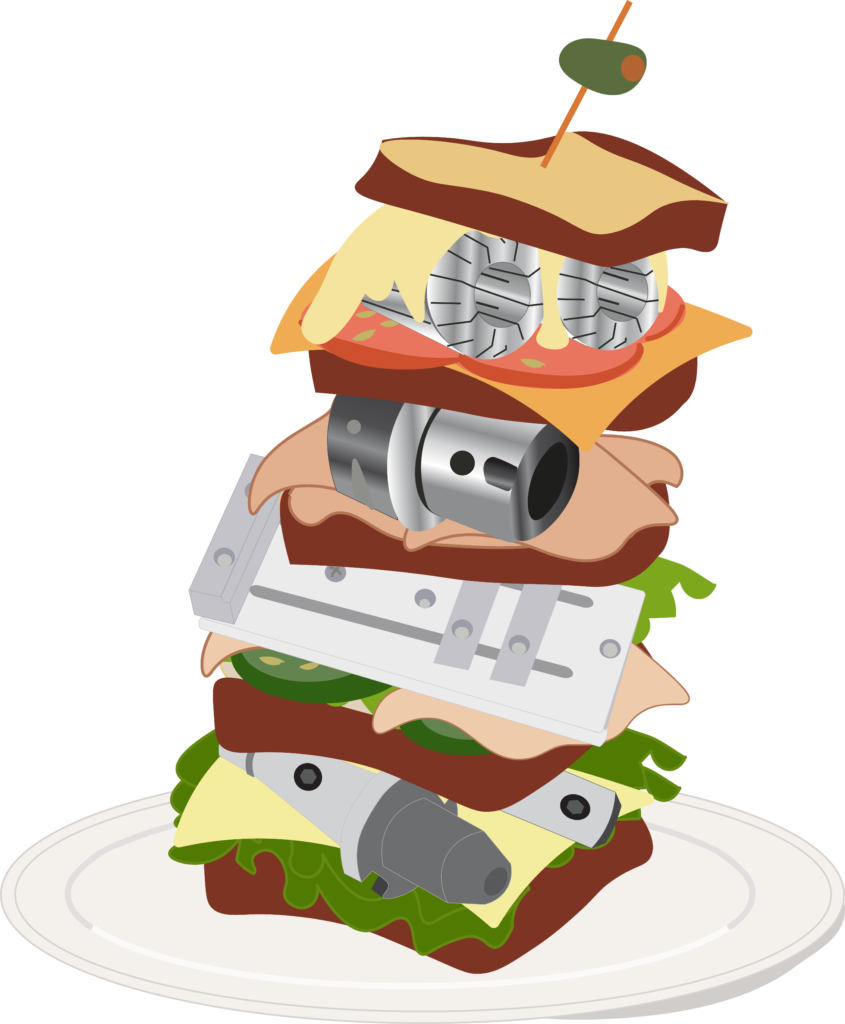
The machine spindle and the table make up the sandwich “bread”, while the sandwich “fillings” are the holders, tools, the coolant, etc. Russ covered the parts of the sandwich that he always checks to diagnose any tooling problem he encounters.
Spindle
Several times Russ has gone into accounts and finds the exact machine, using the same clamps, does not work in a different shop. In these cases, Russ examines the spindle and drawbar first.
The drawbar pulls the spindles or tool holder into the spindle taper. If the drawbar force is inadequate, you will have problems with your cutting tools. A dynamometer can also be used to gauge the drawbar pressure.
Tool Holder
The next part of the sandwich is the tool holder. Tool holders are perishable items that must be maintained. Russ looks at the taper on the holder to see if it has chips, if the holder is old, or if the retention knob (pull stud) is worn out.
Russ stresses that the tool holder is critical to successful machining and must be maintained or replaced regularly as tool holders do not last forever. In addition, collet chucks should not be used for endmilling.
Comparing the expense of machines, labor cost and facilities costs, etc., cutting tools actually make up only 3 to 10% of a manufacturer’s annual expenses, depending on the material being cut.
Workholding
Next, he checks to see if the customer is using the proper workholding for the material.
Tool
Using the proper cutting tool is very important. Today’s cutting tools are extremely advanced. 4 flute tools are becoming a thing of the past, and 5, 6, 7, 9, 11, and 13 flute tools are the future. Combined with Dynamic Milling, productivity, capacity, and profit will increase. It is highly recommended that you clamp tools securely using high-precision collets, milling chucks, hydraulic holders, and finally side lock holders for the best results.
“Workpiece preparation, and workholding, are critical to making accurate parts,” said Russ. “If the part is not prepared correctly in the first operation, it will come back to haunt you in the last. Proper workpiece preparation will allow secure clamping in vises or fixtures, which will insure success.”
Coolant
Coolant concentration is critical to tool life. Tools will fail prematurely if the coolant is not maintained correctly. Tool life can double when maintained.
“For aluminum, concentration of coolant should be around 3 to 5%,” said Russ. “Then when you start cutting hard materials, you need to be up to in the 12 to 15% range.”
Helping Manufacturers Succeed
Russ’ job goes beyond simply troubleshooting tools. He goes the extra mile to provide customers insight on how to improve their machining processes.
“It’s helpful, if the tool representative that you are working with has machining experience,” said Russ.
Russ had a customer running a large mill part with ceramic tools. Ceramic tools run very hot, so hot that the parts were warping during machining and had to be left to cool for two days, then be machined flat. This led to inconsistent part quality and tons of wasted time for the customer. To resolve this, Russ recommended multi flute tools and Dynamic Milling principles to keep the part cool.
“The part came out flat within .002 and the customer was awarded a multi-million dollar contract,” added Russ.
Russ gets his customers up to speed with Mastercam. Having been an active Mastercam user since Version 5.5, Russ offers machinists a new perspective on how to program their tools and always stresses the importance of how evolutions in CAD/CAM technology influence machine tools.
Another oversight Russ has seen all-too-often is using coolant with insertable cutters for steel parts. Insertable cutters should be run dry (without coolant) at higher speeds and feeds. Using coolant with an insertable cutter can cause thermal cracking, wearing them out prematurely*.
*This does not apply to Superalloys such as titanium, and inconel.
Using the correct speeds, feeds, insert grade, and chip breakers while running dry will increase tool life and productivity by 30 to 60 percent.
Get in Touch with a Tool Rep
Talking to a Tooling Representative is crucial to ensuring that you get the maximum benefit out of the tools you use to keep your shop profitable. To get in touch with a tooling representative, you can call the manufacturer directly. Or, you can call a local tooling agency, like Western Tool & Supply, to have them send out a representative to help with your specific tooling needs.
To get in touch with Russ Johnson specifically, contact Western Tool & Supply or connect with him on Linkedin!
Follow MCAM Northwest!
Facebook: @MCAMNorthwest
LinkedIn: mcam-northwest
Twitter: @MCAM_NW
YouTube: The MCAM Northwest
To view and register for upcoming MCAM Northwest Mastercam webinars, visit our Events page.